*Desarrollo del sistema de automatización control de planta de producción dedicada al cuidado personal y cuidado del hogar
Con sede en Colombia reconocida multinacional apertura una nueva planta de producción dedicada a la comercialización de productos de consumo masivo para el exigente sector del cuidado personal y cuidado del hogar.
Dentro de sus líneas de producción se encuentran productos de Cuidado Personal Líquidos (Personal Care) como Shampoo, Acondicionador, Crema de Peinar para el cabello y de productos de Cuidado del Hogar Líquidos (Home Care) como Suavizante de Ropa.
ProcessPack ha diseñado un modelo metodológico el desarrollo de proyectos basados en PlantPAx de Rockwell Automation, plataforma que integra programación de PLC basada en Add-Ons Instructions y faceplates de HMI para la puesta en servicio de módulos y equipos de control. PlantPAx es una plataforma que cumple con múltiples estándares de automatización como ISA-18.2, ISA-88, ISA-95 e ISA-101. Estas herramientas preconfiguradas permiten una ingeniería limpia y eficiente, con tiempos de comisionamiento óptimos, mejor interacción y adaptación del usuario final
El proyecto fue estructurado dentro de la norma ISA-88 para el desarrollo de sistemas de control tipo batch. Parte del trabajo estuvo orientado al desarrollo de sistemas de control utilizando programación de módulos de control, módulos de equipo y fases de operación en los diversos PAC provistos. Dado que se trata de una ingeniería modular, el grupo de trabajo puede realizar tareas concurrentes en diferentes niveles, como en sistemas producción basados en batch donde se implementarán los modelos batch de las plantas, las clases y las recetas maestras; servidores de información para todo el tratamiento, seguimiento y auditoría de procesos y sistemas de visualización de eventos de planta basados en SCADA y reportes.
Para la implementación del proyecto han sido dispuestos 9 servidores, diversos switches administrables con cableado de red con enlaces redundantes o en anillo, 2 estaciones de operador con acceso a todos los recursos de control de la planta, 1 estación de ingeniería para gestión centralizada de cambios de recetas, políticas de manejo y actualizaciones de programa, 6 skid para CIP integrados al sistema de control central, redes AS-Interface para control de válvulas con eficiencia de cableado, válvulas Mix-Proof con control de limpieza de sellos a lo largo de toda la planta y variadores de velocidad con comunicación EtherNet/IP para la mayoría de los motores.
Desafío:
- Implementación de un sistema de control Batch para 4 Líneas de producción en 2 áreas, con incorporación de CIP. El sistema debe permitir implementación de recetas de usuario y producto con generación de reportes, registro histórico de variables de planta, administración de usuarios y gestión de activos de automatización.
- Trazabilidad de todas las acciones de manufactura con registro de variables, acciones ejecutadas por usuarios, cambios de parámetros, actualización de recetas y cambios de programas.
- Arquitectura robusta de alta disponibilidad, flexible y escalable.
Solución:
- Arquitectura distribuida utilizando FactoryTalk y Logix 5000 soportado por una red de comunicaciones EtherNet/IP.
- Gestión de usuarios y servicios bajo dominio de Windows usando Active Directory
- Aplicación de las librerías PlantPAx 3.5 para desarrollo de lógica de control de equipos, rutinas de proceso y visualización en HMI.
- Generación de mímicos de planta usando FactoryTalk View Site Edition en configuración distribuida.
- Control de producción con generación de reportes usando FactoryTalk Batch y MS-SQL Standard
- Registro histórico de variables y presentación de reportes de tendencias usando FactoryTalk Historian SE y FactoryTalk VantagePoint EMI
- Gestión de activos de automatización con auditoria de accesos y control de cambios mediante FactoryTalk AssetCentre
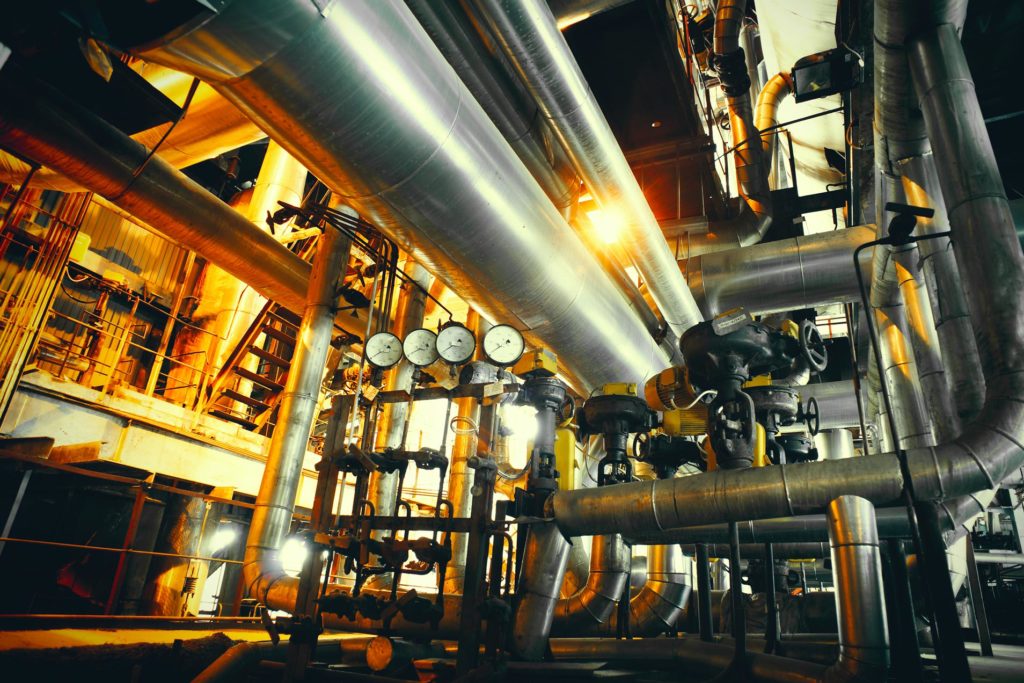
Resultados:
- Sistema de control y automatización conformado por 2 PLC maestros para control de producción, 9 servidores dedicados para cada función del sistema (Control de Dominio, Bases de datos, Proceso y HMI, Producción por Lotes, Registro histórico, Control de activos y Medición de Energía). El sistema puede ser accedido por 2 estaciones de operación en el cuarto de control, una estación de ingeniería y 16 estaciones de campo con acceso por usuario.
- Red de control basada en EtherNet/IP resiliente mediante redundancia de rutas, comunicación en anillo, redundancia de enlaces, detección bucles, gestión de tráfico mediante VLANs y etiquetamiento de dispositivos finales.
- SCADA con mímicos de planta y pantallas de operación estándar a lo largo de toda la planta. Desde este el operador puede ejecutar recetas batch y operaciones por fases de forma consistente y segura.
- Gestión centralizada de alarmas, eventos, recetas, reportes de producción, tendencias históricas y copias de respaldo de programas.
- Diseño escalable listo para integración con la red corporativa de la planta.
- Registro histórico dedicado de variables de proceso con presentación de reportes via web.
- Gestión centralizada de políticas de seguridad con control de acceso por usuarios, administración de privilegios según perfiles, auditoria de cambios de programas de automatización y copias de respaldo con control de versiones.